6063/T5 Alüminyum Boru
6063 alüminyum alaşımı, alüminyum kapı, pencere ve perde duvar çerçevelerinin yapımında yaygın olarak kullanılmaktadır.Yaygın bir alüminyum alaşımlı modeldir.
Ürün Açıklaması
6063 alüminyum alaşımı
6063 alüminyum alaşımı, alüminyum kapı, pencere ve perde duvar çerçevelerinin yapımında yaygın olarak kullanılmaktadır.Yaygın bir alüminyum alaşımlı modeldir.
- Çince adı: 6063 alüminyum alaşımı
- Kullanımı: Alüminyum kapılar, pencereler ve giydirme cephe çerçeveleri oluşturmak
- Bileşim: AL-Mg-Si
giriiş
Kapı, pencere ve giydirme cephelerin yüksek rüzgar basıncı direncine, montaj performansına, korozyon direncine ve dekorasyon performansına sahip olmasını sağlamak için alüminyum alaşımlı profillerin kapsamlı performansına yönelik gereksinimler, endüstriyel profillere yönelik standartlardan çok daha yüksektir.Ulusal standart GB/T3190'da belirtilen 6063 alüminyum alaşımının bileşim aralığı dahilinde, kimyasal bileşimin farklı değerleri, farklı malzeme özelliklerine yol açacaktır.Kimyasal bileşim geniş bir aralığa sahip olduğunda performans farkı geniş bir aralıkta dalgalanacaktır., Böylece profilin kapsamlı performansı kontrolden çıkacaktır.
Kimyasal bileşim
6063 alüminyum alaşımının kimyasal bileşimi, yüksek kaliteli alüminyum alaşımlı yapı profillerinin üretiminin en önemli parçası haline gelmiştir.
performans etkisi
6063 alüminyum alaşımı, AL-Mg-Si serisinde orta mukavemetli, ısıl işlem görebilen ve güçlendirilmiş bir alaşımdır.Mg ve Si ana alaşım elementleridir.Kimyasal bileşimi optimize etmenin ana görevi, Mg ve Si yüzdesini belirlemektir (kütle oranı, aşağıda aynıdır).
1. 1Mg Mg ve Si'nin rolü ve etkisi, Mg2Si güçlendirme aşamasını oluşturur.Mg içeriği ne kadar yüksek olursa, Mg2Si miktarı da o kadar fazla olur, ısıl işlemin güçlendirme etkisi o kadar büyük olur, profilin çekme mukavemeti o kadar yüksek olur ve deformasyon direnci o kadar yüksek olur.Arttıkça alaşımın plastisitesi azalır, işleme performansı bozulur ve korozyon direnci bozulur.
2.1.2 Si'nin rolü ve etkisi Si miktarı, Mg'nin rolünün tam olarak uygulanmasını sağlamak için alaşımdaki tüm Mg'nin Mg2Si fazı formunda bulunmasını sağlamalıdır.Si içeriği arttıkça alaşım taneleri incelir, metal akışkanlığı artar, döküm performansı iyileşir, ısıl işlem güçlendirme etkisi artar, profilin çekme mukavemeti artar, plastisite azalır ve korozyon direnci bozulur.
3.İçerik seçimi
4.2.1Mg2Si miktarının belirlenmesi
5.2.1.1 Mg2Si fazının Mg2Si alaşımındaki rolü, sıcaklıktaki değişikliklerle alaşımda çözünebilir veya çökelebilir ve alaşımda farklı formlarda bulunur: (1) Dağınık faz β'' Mg2Si fazı katı çözeltide çökeltilir Dağılımlı parçacıklar artan sıcaklıkla büyüyecek kararsız bir fazdır.(2) Geçiş fazı β', sıcaklığın artmasıyla da büyüyecek olan β'' büyümesiyle oluşan bir ara yarı kararlı fazdır.(3) Çöken faz β, çoğunlukla tane sınırları ve dendrit sınırlarında yoğunlaşan β'fazının büyümesiyle oluşan kararlı bir fazdır.Mg2Si fazının güçlendirme etkisi, β'' dağınık faz halindeyken, β fazının β'' fazına dönüştürülmesi işlemi güçlendirme işlemidir ve bunun tersi de yumuşama işlemidir.
2.1.2 Mg2Si miktarının seçimi 6063 alüminyum alaşımının ısıl işlem güçlendirme etkisi Mg2Si miktarının artmasıyla artar.Mg2Si miktarı %0,71 ila %1,03 aralığında olduğunda, Mg2Si miktarının artmasıyla çekme mukavemeti yaklaşık olarak doğrusal olarak artar, ancak deformasyon direnci de artarak işlemeyi zorlaştırır.Ancak Mg2Si miktarının %0,72'den az olması durumunda, ekstrüzyon katsayısı küçük (30'dan küçük veya eşit) ürünler için çekme mukavemeti değeri standart gereklilikleri karşılamayabilir.Mg2Si miktarı %0,9'u aştığında alaşımın plastisitesinde azalma eğilimi görülür.GB/T5237.1-2000 standardı, 6063 alüminyum alaşımlı T5 profilinin σb'sinin ≥160MPa ve T6 profilinin σb≥205MPa olmasını gerektirir ve bu pratikle kanıtlanmıştır.Alaşımın çekme mukavemeti 260MPa'ya kadar ulaşabilir.Ancak seri üretime etki eden pek çok faktör var ve hepsinin bu kadar yüksek bir düzeye ulaşmasını sağlamak mümkün değil.Kapsamlı olarak dikkate alındığında, ürünün standardın gerekliliklerini karşıladığından emin olmak için profilin yüksek mukavemetli olması gerekir, aynı zamanda üretim verimliliğini artırmaya yardımcı olacak şekilde alaşımın ekstrüde edilmesi kolay olmalıdır.Alaşımın mukavemetini tasarlarken T5 halinde teslim edilen profil için tasarım değeri olarak 200MPa alıyoruz.Şekil 1'den çekme mukavemeti yaklaşık 200 MPa olduğunda Mg2Si miktarının yaklaşık %0,8 olduğu görülmektedir.T6 durumundaki profil için çekme mukavemetinin tasarım değerini 230 MPa olarak alıyoruz ve Mg2Si miktarı 0,95'e çıkarılıyor.%.
2.1.3 Mg içeriğinin belirlenmesi Mg2Si miktarı belirlendikten sonra Mg içeriği şu şekilde hesaplanabilir: %Mg=(1,73×Mg2Si%)/2,73
2.1.4 Si içeriğinin belirlenmesi Si içeriği, tüm Mg'nin Mg2Si oluşturması şartını karşılamalıdır.Mg2Si'deki Mg ve Si'nin bağıl atom kütle oranı Mg/Si=1,73 olduğundan temel Si miktarı Si bazı=Mg/1,73 olur.Ancak uygulama, harmanlama için Si bazının kullanılması halinde, üretilen alaşımın çekme mukavemetinin genellikle düşük ve niteliksiz olduğunu kanıtlamıştır.Açıkçası alaşımdaki yetersiz Mg2Si miktarından kaynaklanmaktadır.Bunun nedeni alaşımdaki Fe ve Mn gibi yabancı maddelerin Si'yi çalmasıdır.Örneğin Fe, Si ile bir ALFeSi bileşiği oluşturabilir.Bu nedenle, Si kaybını telafi etmek için alaşımda fazla Si bulunması gerekir.Alaşımdaki fazla Si aynı zamanda çekme mukavemetinin arttırılmasında tamamlayıcı bir rol oynayacaktır.Alaşımın çekme mukavemetindeki artış, Mg2Si ve fazla Si'nin katkılarının toplamıdır.Alaşımdaki Fe içeriği yüksek olduğunda Si, Fe'nin olumsuz etkilerini de azaltabilir.Ancak Si, alaşımın plastisitesini ve korozyon direncini azaltacağından Si fazlalığının makul şekilde kontrol edilmesi gerekir.Gerçek deneyime dayanarak fabrikamız fazla Si miktarını %0,09 ila %0,13 aralığında seçmenin daha iyi olduğuna inanmaktadır.Alaşımdaki Si içeriği şu şekilde olmalıdır: %Si=(Si baz + Si üzeri)%
Kontrol aralığı
3.1 Mg Mg'nin kontrol aralığı, eritme işlemi sırasında yanacak olan yanıcı bir metaldir.Mg'nin kontrol aralığı belirlenirken yanmadan kaynaklanan hata dikkate alınmalı ancak alaşım performansının kontrolden çıkmasını engelleyecek kadar geniş olmamalıdır.Tecrübemiz ve fabrikamızın içerik seviyesi, eritme ve laboratuvar testleri temelinde, Mg'nin dalgalanma aralığını %0,04, T5 profilini %0,47 ila %0,50 ve T6 profilini %0,57 ila %0,50 aralığında kontrol ettik.%60.
3.2 Si'nin kontrol aralığı Mg'nin aralığı belirlendiğinde Si'nin kontrol aralığı Mg/Si oranıyla belirlenebilir.Fabrika Si'yi %0,09 ile %0,13 arasında kontrol ettiğinden, Mg/Si'nin 1,18 ile 1,32 arasında kontrol edilmesi gerekir.
3.3 36063 alüminyum alaşımı T5 ve T6 durum profillerinin kimyasal bileşiminin seçim aralığı.Alaşım bileşimini değiştirmek istiyorsanız, örneğin T6 profillerin üretimini kolaylaştırmak için Mg2Si miktarını %0,95'e çıkarmak istiyorsanız, Mg'yi üst kısım boyunca yaklaşık %0,6'lık bir konuma taşıyabilirsiniz. ve Si'nin alt sınırları.Şu anda Si yaklaşık %0,46, Si %0,11 ve Mg/Si 1'dir.
3.4 Son açıklamalar Fabrikamızın deneyimine göre, 6063 alüminyum alaşımlı profillerdeki Mg2Si miktarı %0,75 ila %0,80 aralığında kontrol edilmektedir ve bu, mekanik özelliklerin gerekliliklerini tam olarak karşılayabilmektedir.Normal ekstrüzyon katsayısı durumunda (30'dan büyük veya buna eşit), profilin çekme mukavemeti 200-240 MPa aralığındadır.Ancak alaşımın bu şekilde kontrol edilmesi yalnızca iyi plastikliğe, kolay ekstrüzyona, yüksek korozyon direncine ve iyi yüzey işleme performansına sahip olmakla kalmaz, aynı zamanda alaşım elementlerinden de tasarruf sağlar.Ancak Fe safsızlığının sıkı bir şekilde kontrol edilmesine özel dikkat gösterilmelidir.Fe içeriği çok yüksekse ekstrüzyon kuvveti artacak, ekstrüde edilen malzemenin yüzey kalitesi bozulacak, anodik oksidasyon renk farkı artacak, renk koyu ve donuk olacak, Fe ayrıca plastisite ve korozyon direncini azaltacaktır. alaşımdan.Uygulama, Fe içeriğini %0,15 ila %0,25 aralığında kontrol etmenin ideal olduğunu kanıtlamıştır.
Kimyasal bileşim
Si | Fe | Cu | Mn | Mg | Cr | Zn | Ti | Al |
0,2~0,6 | 0,35 | 0.10 | 0.10 | 0,45~0,9 | 0.10 | 0.10 | 0.10 | Marj |
Mekanik özellikler:
- Çekme mukavemeti σb (MPa): ≥205
- Uzama gerilimi σp0,2 (MPa): ≥170
- Uzama δ5 (%): ≥7
Yüzey korozyonu
6063 alüminyum alaşımlı profillerin silikondan kaynaklanan korozyon davranışı önlenebilir ve kontrol edilebilir.Hammadde alımı ve alaşım bileşimi etkili bir şekilde kontrol edildiği sürece, magnezyumun silikona oranı 1,3 ila 1,7 aralığında sağlanır ve her prosesin parametreleri sıkı bir şekilde kontrol edilir., Silikonun ayrışmasını ve serbest kalmasını önlemek için, silikon ve magnezyumun faydalı bir Mg2Si güçlendirme fazı oluşturmasını sağlamaya çalışın.
Bu tür silikon korozyon lekeleri bulursanız yüzey işlemine özellikle dikkat etmelisiniz.Yağdan arındırma ve yağdan arındırma sürecinde zayıf alkali banyo sıvısı kullanmaya çalışın.Eğer şartlar uygun değilse asitli yağ alma sıvısında da bir süre bekletmeniz gerekir.Mümkün olduğu kadar kısaltmaya çalışın (nitelikli alüminyum alaşımlı profil, asit yağ giderme çözeltisine 20-30 dakika, sorunlu profil ise yalnızca 1 ila 3 dakika yerleştirilebilir) ve sonraki pH değerini yıkama suyunun daha yüksek olması (pH>4, kontrol Cl- içeriği), alkali korozyon prosesinde korozyon süresini mümkün olduğu kadar uzatması ve ışığı nötralize ederken nitrik asit lüminesans solüsyonu kullanması gerekir.Sülfürik asit anodize edildiğinde, silikonun neden olduğu koyu gri korozyon noktalarının belirgin olmaması için mümkün olan en kısa sürede enerjilendirilmeli ve oksitlenmelidir. Kullanım gereksinimlerini karşılayabilir.
Detay Gösterimi
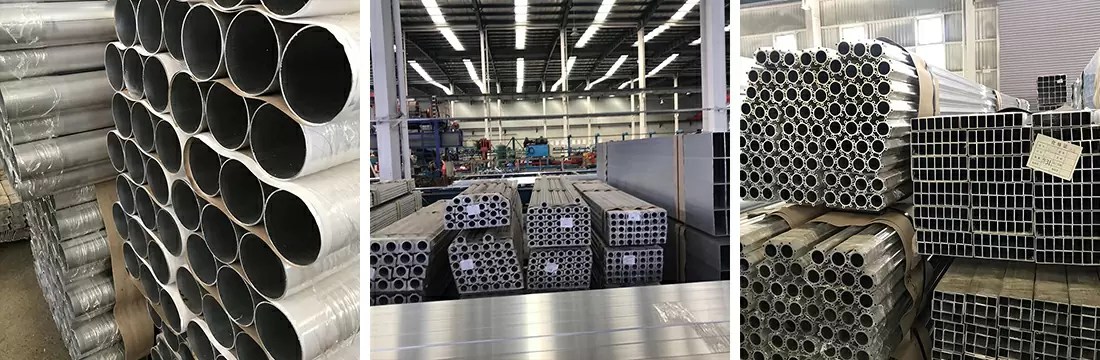
Gönderim zamanı: 28 Kasım 2022